Our close, longstanding partnerships with airports all over the world have taught us a great deal, not least that the needs of every airport are different. Of all the production lines within the group, airport equipment requires a particularly wide variety of custom designs. We take a look behind the scenes.
Our St. Blasien plant has been manufacturing snow-clearing equipment and machinery for airports for over 60 years. From the very outset, such airport equipment has been custom-made and specifically adapted to the conditions at the respective airport – a feat requiring considerable engineering skill. This has remained the standard to this day. In the airport business, we tend to talk about projects rather than products. Line assembly takes place in five cycles. Components and modules are pre-assembled in several places, while the carrier vehicles are converted and prepared separately in the lead-up to the first cycle.
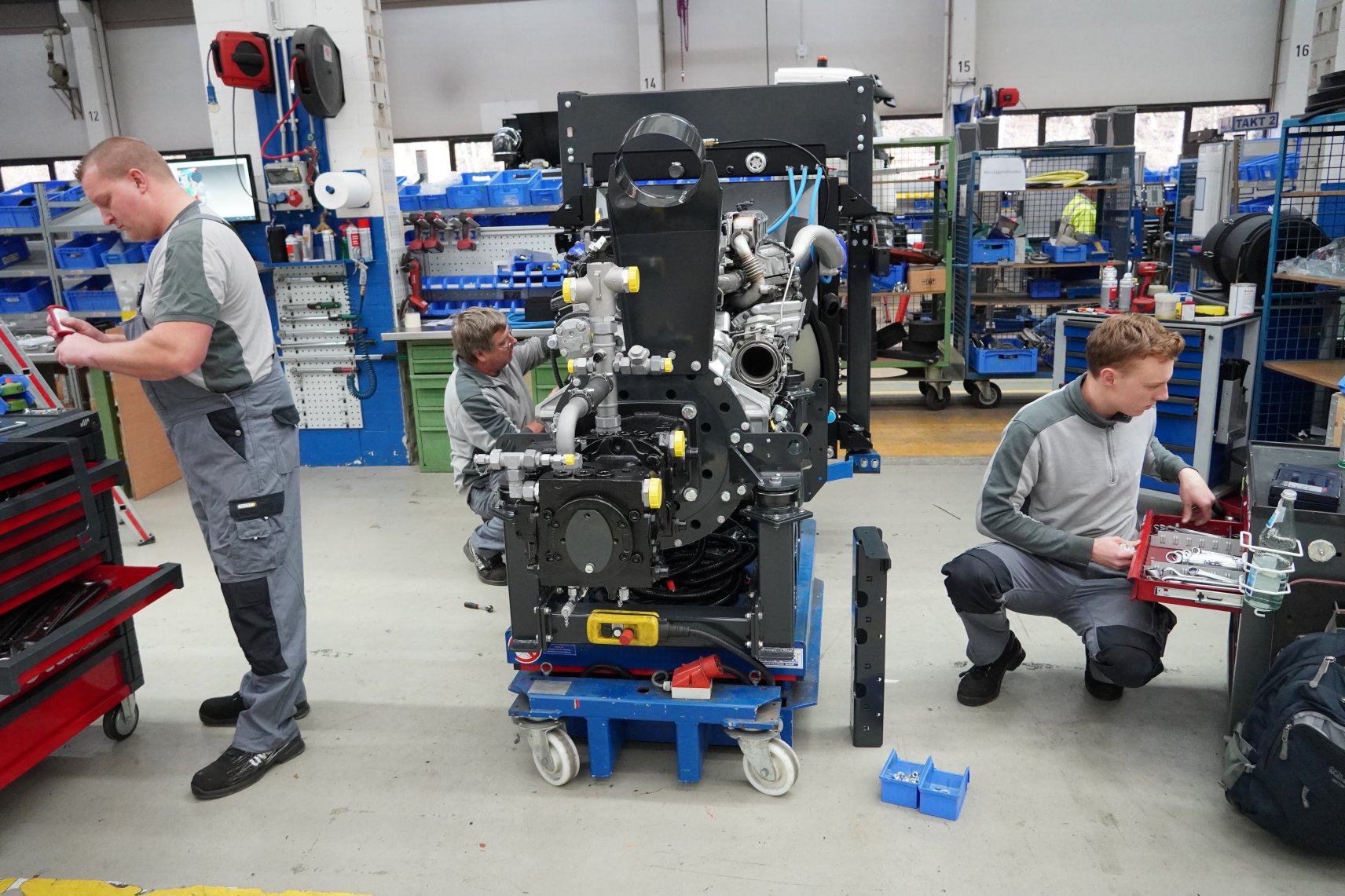
Pre-assembly of the ASC 990 drive unit
Wolfgang Kiefer oversees the assembly of project products at the St. Blasien plant. A qualified vehicle electrician, he has been with the company for 21 years. ‘Our work is very varied because every machine is unique. This requires a high degree of teamwork, because we can only get things to production if our order management, procurement, design and quality management teams are working together smoothly,’ says Wolfgang. It’s a somewhat surprising admission, but a telling one. In the airport business, and even in the assembly team itself, teamwork is a driving concern, alongside the interaction of mechanics, hydraulics, pneumatics and electrics, and making sure that all the elements align with the various engine manufacturers and emission standards. Wolfgang attaches great importance to the high level of professional qualifications among the team. ‘Ultimately, our staff on the line and from the whole team form the foundation and key to our success. Only by working as a team can we fulfil our promise to improve performance for our customers by offering them reliable solutions and excellent service.
Recent challenges have put more of a strain on the production line for airport equipment: the disruption to supply chains during the pandemic made it even more difficult to build the equipment to the required timelines. When asked about this, Wolfgang points out that many issues that had seemed insurmountable at the outset were ultimately overcome thanks to close coordination and cooperation both internally and with customers. ‘Ongoing optimisation of production has always been an integral part of our work. We are currently working to make material flows even more transparent so that we can ultimately react even faster and more efficiently to interruptions, which will probably continue for a while due to the situation in the procurement markets.
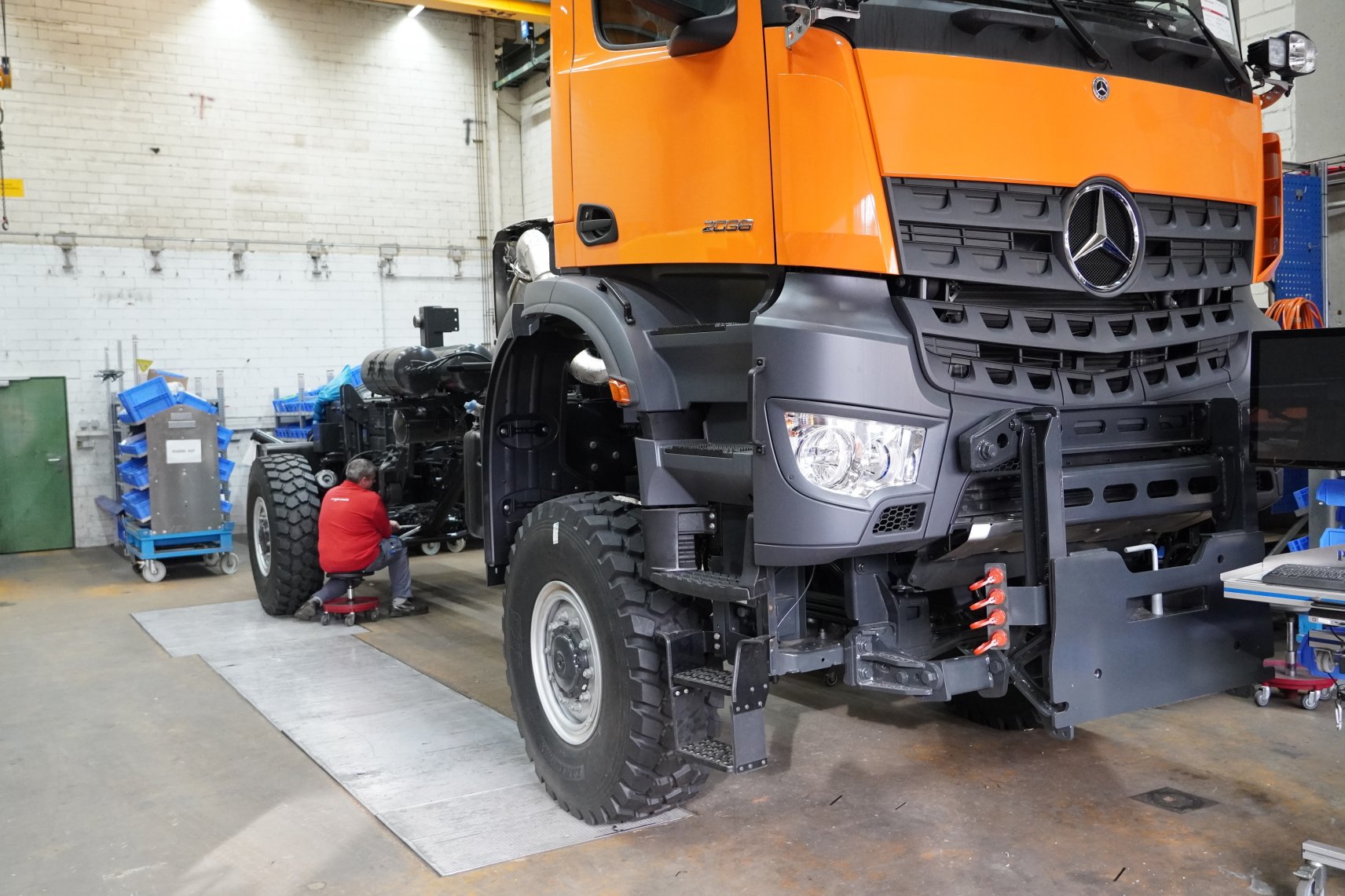
Assembly and preparation of a carrier vehicle
However, it was then engineering pride that came up as he continues to talk. While it had previously been standard to first convert the carrier vehicle and to prepare it for the various devices, last year trucks were purchased in assembly kits for the first time and put together directly. From the outside, this might look like a straightforward gain in efficiency, but it represented a demanding yet exciting challenge for the team. Wolfgang describes it as ‘a colossal team effort’. The ingenuity for which the Black Forest region is famous laid the foundations for this success 60 years ago, and every single machine that leaves the St. Blasien factory still has it in spades.
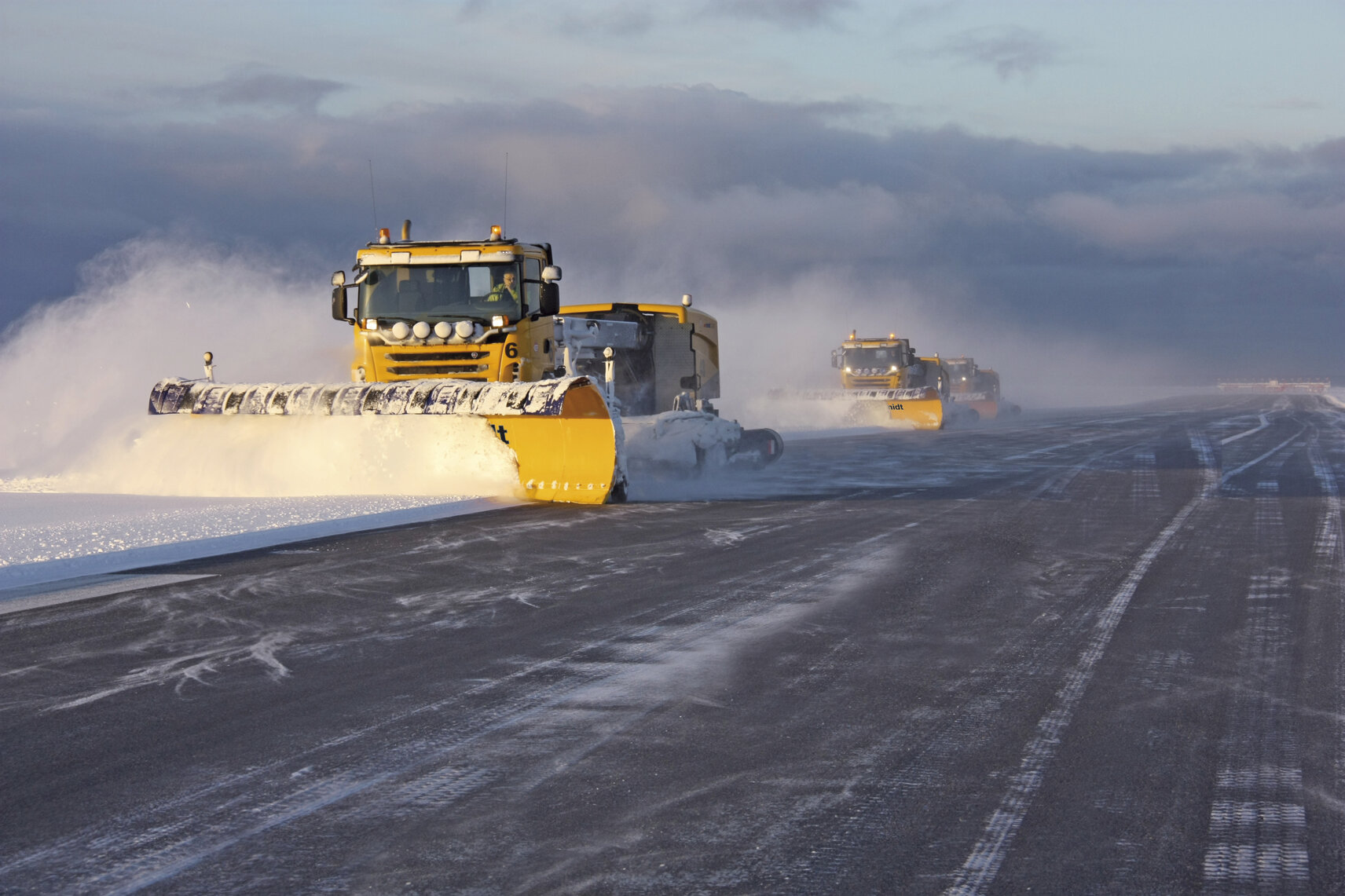
Schmidt TJS in operation