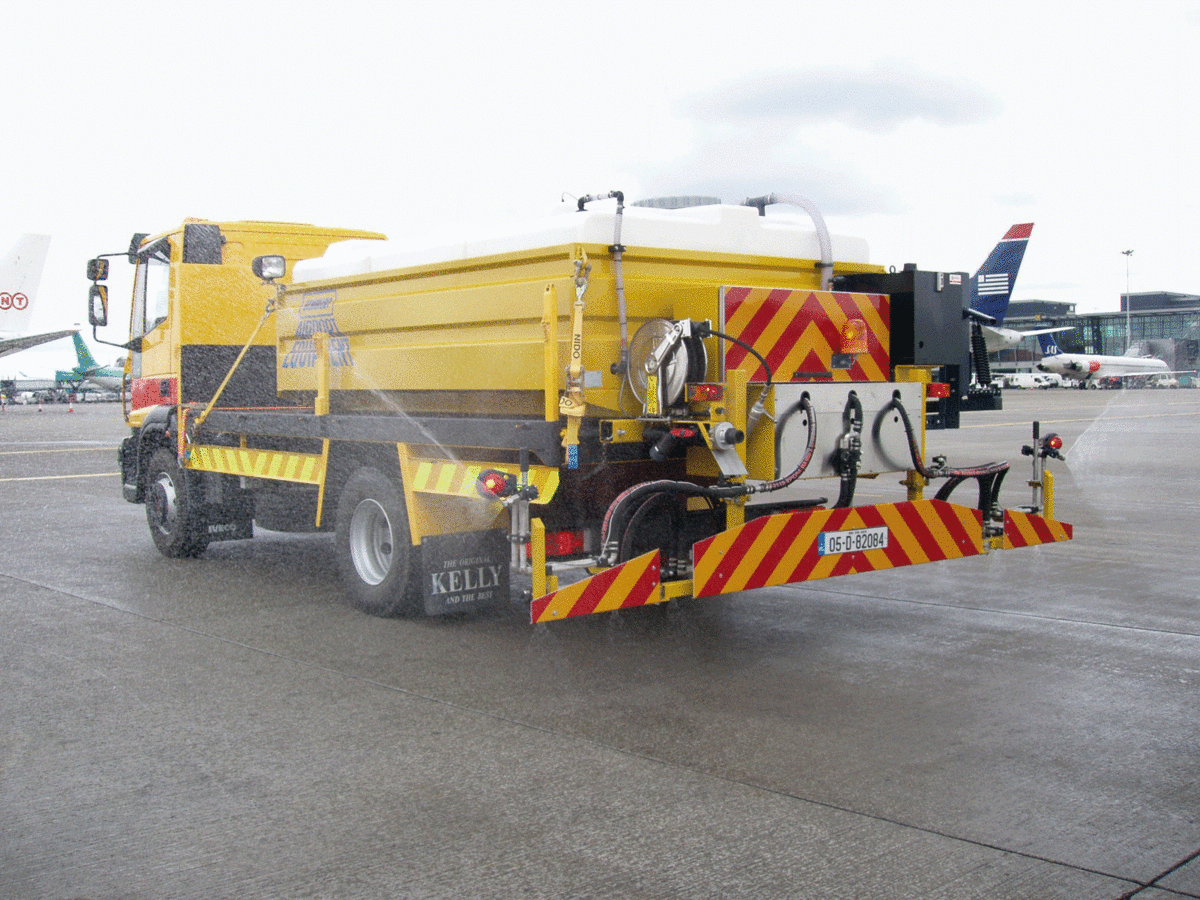
Airport Sprayer
The WSP was developed for the de-icing of airport aprons. Its spray and projection nozzles guarantee highly accurate distribution of the de-icing liquid. The maximum spraying width is 20 metres.
Construction and Technology
The WSP is comprised of three components: the modular polyethylene fluid tanks, the drive unit on the vehicle axle (Roto-Power), as well as, a rear-mounted spray bar with spray nozzles and projection nozzles. The high-quality air-injected nozzles are set in a row located on the spray bar. One projection nozzle is located on each upper side of the spray bar ends. The entire machine is coated with a specially developed corrosion protection. All cavities are air closed. The spray tubes are made of stainless steel. The sprayer is designed for mounting on light, medium and heavy carrier vehicles. The WSP’s modular design offers a wide variety of assembly options. This means that it can be easily customised to meet the individual needs of the various airports. For example, mounting the sprayer on the carrier vehicle can either be done via a fix-mount or de-mountable system.
In Operation
The WSP tackles icy surfaces using anti-icing and de-icing methods at a road speed related operating speed of 12 to 18 km/h. Due to its narrowness without the lateral spraying arms and its high manoeuvrability, the WSP is ideal for use on airport aprons. The spraying width of the rear spray bar is 4 m. An asymmetric spraying width of 12 m is achieved by turning on one of the two lateral wide-spray nozzles. The maximum spraying width of 20 m is attained by activating the second lateral projection nozzle on the other side of the spray bar. The feeding of the de-icing liquid to the nozzles is done by three road speed related control driven pumps. Both of the projection nozzles are each regulated by a pump and the third pump supplies the spray nozzles. Up to 20 g/m² of the de-icing liquid can be sprayed with good and efficient coverage. The unique Schmidt low-pressure pump system with its air-injected nozzles provides low spraying pressure during operation. The nozzles at the rear are positioned just 300 mm above the surface of the ground and form large drops. This reduces the swirling caused by turbulence to a minimum. Spraying is controlled by the control panel which is very easy to operate and located in the operator’s cabin. This means that both the spraying width and dosage can be regulated quickly and efficiently.